Other Coating Processes
Partner with RDC Coatings for environmentally friendly formulations that enhance your application process and finished products.
Whatever the application method, let RDC Coatings create a formulation that delivers superior physical properties and boosts operational efficiencies.
In addition to creating energy cured coatings for roll coating, curtain coating, spray coating, and vacuum coating operations, RDC engineers a range of environmentally friendly custom coatings suitable for many other application processes. Your specially formulated, energy cured coating — such as ultraviolet (UV), Excimer UV, electron beam (EB) — will meet the specific requirements of your finishing line and products.
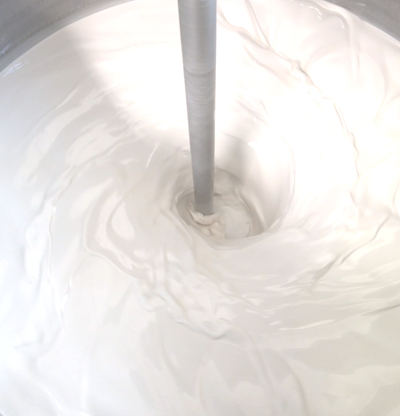
Dip Coating
This process creates thin film coatings on materials, particularly those with highly irregular or multi-faceted surfaces. It’s a technique that involves immersing the object or substrate into a vat or tank of coating material, removing it, and then drying it. The coating thickness depends on several factors, including the viscosity of the solution, immersion time, withdrawal speed, evaporation rate, and curing methodology.
Gravure Coating
This process uses an engraved roller to apply an energy cured coating to a thin, flexible material like fabric, foil, or film. The roller is first run through a coating bath, which fills the engraved lines or dots of the roller with the coating material. After a blade removes excess coating from the roller, the coating is deposited onto the substrate as it passes between the engraved roller and a backup roll. The material then passes through the curing system to harden the coating.
Web Coating
Frequently used in printing, this process applies a fine layer of liquid coating to a long, thin substrate such as foil, paper, or film. The material typically passes through multiple rollers, the last of which applies the final energy cured coating before it passes through the curing system.
Edge Coating
Also known as stripe coating, this process applies the energy cured coating only to the edge of the substrate. This is often done to seal the edge for waterproofing or to prevent corrosion. It is often used in an in-line production process.
Benefits of your RDC Coatings’ energy cured coating chemistries.
Partner with RDC Coatings for coating solutions that meet the specific requirements of your manufacturing process, application and curing systems, environment, and product.
Coatings Engineered to Optimize Your Production Process
Considering changing your existing coating formula, developing new finish options for your customers, or designing a new production line? Turn to RDC’s customer-focused expertise for help. Your formulation begins with an on-site process audit conducted by RDC to evaluate your coating line and finished products. Informed by those details, RDC’s engineers create your custom coating and verify its performance in state-of-the-art testing labs. RDC also offers process management and technical support services.
Coatings That Enhance Your Application Equipment’s Performance
RDC Coatings’ energy cured formulations are engineered to boost your application equipment’s operation. To improve application consistency, your coating’s rheology is customized for your machinery. Further, your coating can be provided in a variety of container sizes to improve your production line’s efficiency and throughput.
Coating Finishes Formulated for Your Unique Curing Process
Your ultraviolet (UV), Excimer UV, electron beam (EB), or water-based coatings from RDC will yield fast curing, even surfaces in less time. Have a UV curing process already in place? RDC’s UV coatings are designed to perform consistently, whether the UV bulbs are brand new or producing variable doses as they age. RDC’s chemistry delivers better lot-to-lot consistency.
Coatings That Work in Variable Environments
RDC Coatings knows that not every production facility is temperature controlled. Therefore, your coating’s chemistry is engineered for consistent performance across variable humidities and temperatures — from high to low — in all four seasons.
Coating Formulas Tailored to Your Product Specifications
Whatever coating process you use to finish your products, every RDC formulation will match your unique requirements — including complex shapes and large surface areas. Formulations can be created to resist chemicals, scratches, marks, scuffs and abrasions. Other characteristics include enhanced weatherability, a wide range of gloss, better adhesion, and more can be engineered to meet your individual parameters.
Your partner for sustainable, compliant energy-cured finishes
All RDC UV curable finishes are environmentally friendly and comply with globally accepted safety and sustainability standards, including…
- Low or No Volatile Organic Compounds (Low-VOC/Zero-VOC)
- California Air Resources Board (CARB) Compliant
- American Innovation and Manufacturing (AIM) Act Compliant
- Meets or exceeds American National Standards Institute (ANSI), Kitchen Cabinet Manufacturers Association (KCMA), and Scientific Equipment and Furniture Association (SEFA) Testing Requirements
How can RDC Coatings help you?
Manufacturers in multiple industries apply RDC Coatings’ custom formulations to a wide variety of materials and products. Leverage RDC Coatings’ 35-plus years of experience in engineering, developing, and manufacturing custom, energy-cured coatings to address your unique needs.