Other Markets
Your partner for energy cured, high-performance industrial coatings in a variety of applications.
RDC Coatings’ expertise has been leveraged by companies across diverse markets to create custom coating formulations.
As a trusted resource for custom, energy cured coatings used in a range of markets and industries, RDC Coatings has extensive experience creating solutions for unique products and applications. Every RDC finish is custom-formulated to meet the exacting specifications of diverse products and components, delivering high-performance properties that give you a competitive advantage.
These properties can include any desired degree of gloss — from ultra low sheen to high gloss — as well as superior durability through enhanced scratch and abrasion resistance. Your engineered coating will deliver exceptional stain resistance, excellent clarity, and lot-to-lot consistency. Your finish will also be optimized to better support your high throughput, energy cured production process.
Don’t see your industry here? Contact RDC Coatings to speak with an experienced formulations engineer and explore the possibilities for your product. Frequently RDC can create a custom, energy cured coating or finish that will meet your needs — in any market or application.
Electronics
Energy cured coatings for electronic components — such as printed circuit boards, optical fibers, conductor wire, LCD panels, and more — offer faster cures and strong adhesion without the risk of damage associated with thermal drying methods. In addition to offering formulations that improve conductivity and lifespan, RDC can formulate electronics finishes that permit etching, component marking, masking, encapsulating, and conformational coating.
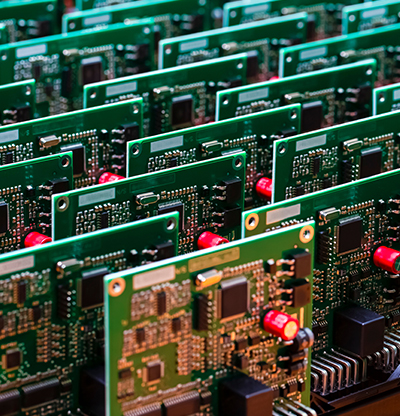
Pipe & Tube
Custom engineered energy cured coatings for plastic, PVC, or metal pipes and tubes from RDC improve durability and provide insulating properties. RDC offers specific formulations for steel, aluminum, and many other metal substrates. Your custom engineered metal coating solution will be formulated to add color, gloss, and slip, scratch, or corrosion resistance to the substrate.
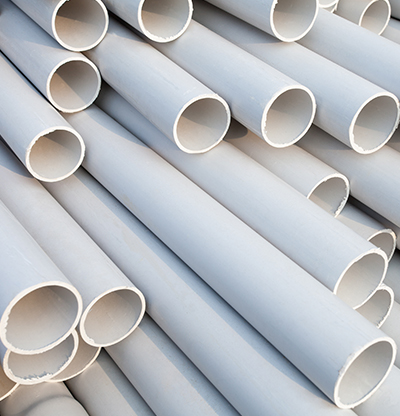
Specialty Paper
To enhance its durability, RDC creates energy cured coatings that are applied to printed specialty papers used in a variety of applications. This includes papers used as wraps for flooring transition strips, picture frames and other composite millwork, as well as window coverings, countertops, and traditional printing of brochures and other collateral. These coatings are engineered to add texture, gloss, and improved resilience against wear.
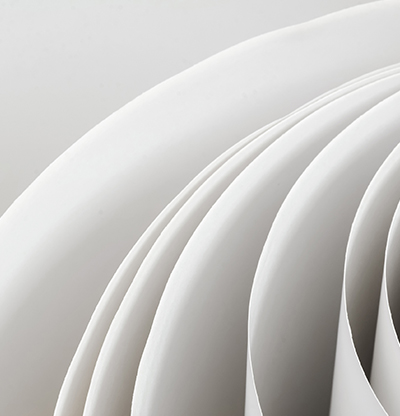
Vinyl
RDC Coatings develops energy cured coatings that meet the exacting specifications of vinyl products (in addition to those found in the flooring industry), including wall coverings, upholstery, decals, wraps, and more. These custom formulated coatings can be used to help the material better withstand scratches, abrasions, scuffs, chemicals, and stains, as well as to increase durability and flexibility.
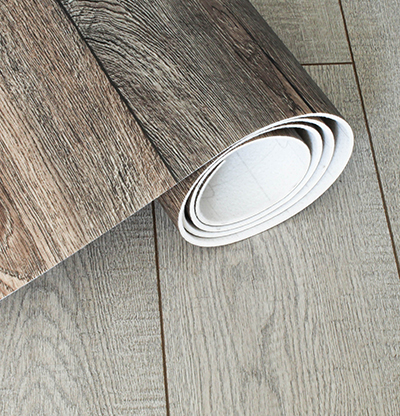
Benefits of your RDC Coatings’ custom engineered finish.
Regardless of your market, your RDC coating solution will match the individual specifications and requirements of your finishing process, application and curing equipment, environment, and product.
Coatings Engineered to Enhance Your Production Process
Looking to augment your current coating formula, offer customers new finish choices, or construct a new manufacturing line? Engage RDC Coatings for customer-focused expertise as a key ingredient in your finishing solution. Every new coating project starts with an on-site process audit to evaluate your current finishing line and products. Based on those details, RDC’s engineers create a custom coating whose performance is confirmed in state-of-the-art testing labs. RDC also provides process management and technical support.
Finishes Designed to Optimize Your Application Equipment
RDC Coatings’ finish solutions are created to optimize your application equipment. Each coating’s rheology provides continuous, smooth flow through roll coating, spray coating, curtain coating, or vacuum coating machines — or other application method. To further improve efficiency and productivity, RDC can supply your coating in a variety of container sizes.
Coatings Created for Your Curing Process
When developing your ultraviolet (UV) curable coating, Excimer UV curable coating, electron beam (EB) curable coating, or water-based coating, RDC’s engineering team seeks formulations that cure quickly and consistently, increasing productivity.
Finishes That Adapt to Changing Environments
Manufacturing operations frequently experience variable temperature and humidity. To compensate for these environmental inconsistencies, RDC engineers your coating to deliver reliable performance throughout the year. Further, RDC’s UV coatings are designed to work consistently, regardless of UV lamp performance and dosage. This ensures that every lot will be the same, whether the bulbs are brand new or not.
Coatings Tailored to Your Requirements
Every coating RDC engineers will match your specifications for appearance and performance. This includes resistance to chemicals, scratches, and abrasions. Other customizable finish characteristics include weatherability, gloss, adhesion, and more.
Your partner for sustainable, compliant energy-cured finishes
All RDC UV curable finishes are environmentally friendly and comply with globally accepted safety and sustainability standards, including…
- Low or No Volatile Organic Compounds (Low-VOC/Zero-VOC)
- California Air Resources Board (CARB) Compliant
- American Innovation and Manufacturing (AIM) Act Compliant
- Meets or exceeds American National Standards Institute (ANSI), Kitchen Cabinet Manufacturers Association (KCMA), and Scientific Equipment and Furniture Association (SEFA) Testing Requirements
How can RDC Coatings help you?
Manufacturers in multiple industries apply RDC Coatings’ custom formulations to a wide variety of materials and products. Leverage RDC Coatings’ 35-plus years of experience in engineering, developing, and manufacturing custom, energy-cured coatings to address your unique needs.