Vacuum Coating
Custom engineered, energy cured finishes that enhance your vacuum coating process.
Leverage RDC Coatings’ expertise in formulating vacuum coatings that deliver consistent, durable finishes.
Proper coating formulation is critical in the effective utilization of vacuum coating equipment, and to the success of the entire high-speed production process. The vacuum coating process efficiently deposits thin layers of coating in-line onto substrates. To solidify the coating on the material, the part passes through an energy curing technology. This process is often employed in industries that finish consistently shaped linear parts, such as millwork, furniture, cabinetry, pipes and tubes, metal, plastic, and more.
RDC Coatings understands the unique requirements and complexities associated with curing your vacuum coated parts. Custom vacuum coating solutions from RDC include stains, sealers, and top coats in both 100% solids and water-based formulations. All are engineered to deliver faster line speeds and shorter cure times, supporting higher throughput. RDC’s coatings can be applied to parts made of a variety of materials, such as vinyl, wood, metal, plastic, or other substrates.
When formulating ultraviolet (UV) curable coatings, Excimer UV curable coatings, electron beam (EB) curable coatings, or water-based coatings for vacuum coating operations, RDC incorporates chemistries that ensure even application. Other key performance factors include strong adhesion to the substrate, a consistent and uniform appearance, minimal drying time, and resistance to chemicals, scratches, and abrasions.
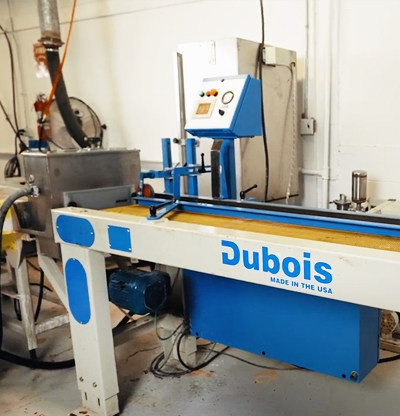
Benefits of your RDC Coatings’ formulations for vacuum coating.
As a trusted supplier of finishes designed for vacuum coating applications, RDC Coatings will deliver solutions that meet the requirements of your production process, application and curing equipment, environment, and product.
Vacuum Coatings Engineered to Improve Your Production Process
Whether you’re considering enhancements to your existing vacuum coating formula, developing new finish offerings, or designing a new production line, RDC will support your coating with customer-focused expertise. Included are initial, on-site process audits that help RDC gain a clear understanding of your coating line and finished products. With those details, RDC’s engineers create your custom vacuum coating formulation and verify its performance across state-of-the-art testing labs. Also, RDC provides routine process management and technical support.
Curtain Coating Formulations Tailored to Your Application Equipment
RDC Coatings’ vacuum coating formulations are custom engineered to improve the operation of your application equipment. To ensure smooth and consistent flow, each coating’s rheology is specifically designed for your machinery. Further, your vacuum coating solution can be packaged in different container sizes, increasing your processes’ efficiency and productivity.
Vacuum Coating Finishes Designed for Your Curing Process
The composition of your ultraviolet (UV), Excimer UV, electron beam (EB), or water-based coatings supports fast curing, even finishes that reduce drying time. Using a UV curing process? RDC’s UV vacuum coatings are engineered to compensate for variable UV dosages, whether the bulbs are brand new or at the end of their usable lifespan. This ensures you achieve better lot-to-lot consistency.
Vacuum Coatings That Deliver a Consistent Finish in Variable Environments
RDC Coatings understands that not every manufacturing facility is climate controlled. Therefore, your vacuum coating’s chemistry is engineered to perform consistently across variable temperatures and humidities — from high to low — year-round.
Vacuum Coating Finishes Formulated to Your Product Parameters
Every coating RDC creates will be formulated to your specific parameters. This includes chemical resistance, scratch and abrasion resistance, weatherability, gloss, adhesion, and more.
Your partner for sustainable, compliant energy-cured finishes
All RDC UV curable finishes are environmentally friendly and comply with globally accepted safety and sustainability standards, including…
- Low or No Volatile Organic Compounds (Low-VOC/Zero-VOC)
- California Air Resources Board (CARB) Compliant
- American Innovation and Manufacturing (AIM) Act Compliant
- Meets or exceeds American National Standards Institute (ANSI), Kitchen Cabinet Manufacturers Association (KCMA), and Scientific Equipment and Furniture Association (SEFA) Testing Requirements
How can RDC Coatings help you?
Manufacturers in multiple industries apply RDC Coatings’ custom formulations to a wide variety of materials and products. Leverage RDC Coatings’ 35-plus years of experience in engineering, developing, and manufacturing custom, energy-cured coatings to address your unique needs.