Electron Beam (EB) Curable Coatings
Your partner for custom engineered, electron beam (EB) curable coatings for any material or process.
Trust RDC Coatings to formulate the EB coating that optimizes your finishing line.
Apply clear and pigmented coatings at greater thicknesses and cured at extremely high speeds — up to 400 feet per minute — with electron beam coating solutions from RDC. Your custom EB coating formulation will be engineered to match the unique specifications of your product and high-speed finishing line. Whether you’re finishing vinyl, wood, metal, plastic, or any specialty substrate, your RDC EB curable coating will be environmentally friendly and comply with globally accepted safety and sustainability standards.
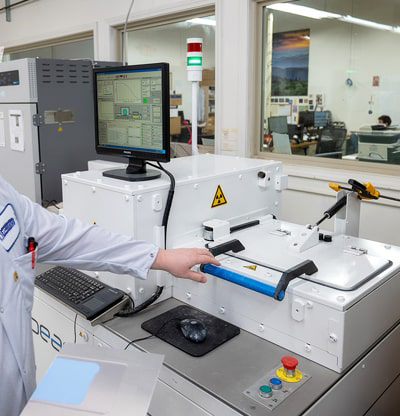
How does EB curing work?
EB curable coatings solidify when exposed to electrons from an electron beam. Because electrons are capable of penetrating any finish, electron beam coatings can be pigmented and applied at greater thicknesses. After the coating is applied in high-speed production lines by one of a variety of methods — including roll coating, spray coating, curtain coating, vacuum coating, and other coating processes— the product passes through an electron beam curing process. There, the electron beam causes the coating to polymerize, instantly transforming it into a high-performance solid surface.
Why use custom-formulated EB curable coatings?
RDC’s custom EB coatings enable manufacturers in a variety of different markets to attain high-performance finishes on a range of products. Your RDC coating will offer significant benefits, such as:
Earth-Friendly, Environmental Advantages
As a green solution, RDC’s electron beam coatings are extremely environmentally friendly. Unlike conventional finishes — which often rely on volatile organic compounds (VOCs) that can contribute to air pollution — EB curable coatings contain little to no VOCs. This makes them a sustainable finishing option by reducing the emission of harmful chemicals into Earth’s atmosphere. Additionally, the EB curing process does not require heat, further minimizing energy consumption and reducing a manufacturer’s carbon footprint.
Enhanced Performance and Durability
Because the electron beam curing process results in a highly cross-linked polymer structure, RDC’s custom EB coatings deliver exceptional performance and durability. They resist abrasions, scuffs, scratches, and chemical exposure, making them ideal for finishing products used in tough applications — including residential and commercial flooring, cabinetry, millwork, hardwood plywood, furniture, and many others. The durability of RDC’s EB coatings can extend the lifespan of these products, minimizing both maintenance costs and the need for frequent reapplications.
Precise Formulations Create Unique Properties
RDC custom engineers every EB curable coating to precisely match the desired properties of your product and its target substrate. Each custom EB formulation meets specific requirements, such as flexibility, hardness, or adhesion to various substrates. These include plastics, metals, wood, vinyl, and specialty materials. The ability to adhere to different materials without compromising the integrity of the substrate or the coating itself makes EB coatings ideal for products in a range of markets, from flooring to plastics.
High-Speed Curing Boosts Production Efficiency
The curing process for EB coatings is incredibly fast, often completed in a matter of seconds. It also allows for all-over curing of highly textured and multi-planed products, where nooks and crannies might not be reached by other curing methodologies. Ideal for high-speed finishing lines, RDC’s custom EB coatings enable manufacturers to significantly reduce cure time and resulting production bottlenecks. Further, EB curing neither requires nor generates heat, eliminating the need for cooling periods and streamlining throughput. Finish defects are also minimized, as this fast-cure method reduces the likelihood of defects such as dust or debris becoming embedded in the coating.
Improved Cost-Effectiveness
While the capital investment in EB curing equipment is significant, the technology offers substantial long-term cost savings. The durability and resilience of RDC’s EB curable coatings reduce the frequency of reapplications and extend the useful life of the product. Additionally, the speed of the curing process minimizes labor costs while increasing throughput, making EB coatings a cost-effective solution for both high-speed and high-volume production lines. The reduction in energy consumption and the elimination of VOC-related regulatory costs further contribute to the overall cost-effectiveness of EB curable coatings.
Benefits of your RDC Coatings’ EB coating formulation.
When you partner with RDC Coatings, your EB curable coating solution is engineered to meet the unique specifications of your production process, application and curing equipment, environment, and the physical properties of your product.
EB Cured Coatings That Enhance Your Electron Beam Process
Whether you’re looking to upgrade your current EB coating formula or designing a new manufacturing line, your EB finish is backed by RDC’s comprehensive, customer-focused expertise. These include initial, on-site process audits to gain a complete understanding of your production line and product. Based on those findings, RDC’s engineers develop a custom EB coating formulation that is subject to proof-of-concept verification in state-of-the-art testing labs. Additionally, RDC provides ongoing process management and technical support.
EB Curable Finishes Formulated for Your Application Equipment
RDC Coatings’ EB curable formulations are optimized for your application equipment. RDC will work with you to define the coating rheology and application parameters that ensure consistent, even finishes. Further, your EB coating solutions can be supplied in different container sizes, boosting your operational efficiency and productivity.
EB Cured Coatings Created to Match Your E-Beam Curing Method
The chemistries used to produce your EB curable coating are activated by electrons generated by any e-beam curing equipment. Comprehensive testing in RDC Coatings’ state-of-the-art labs — and at your site — confirms your custom engineered coating formulation will deliver the performance properties you expect.
EB Coating Formulations That Adapt to Your Variable Environment
RDC Coatings understands that not every manufacturing facility is climate controlled. Therefore, your EB curable coating’s chemistry is engineered to perform consistently across a broad range of temperatures and humidities — from high to low. Additionally, RDC’s EB formulations accommodate variable e-beam source performance, whether brand new or approaching the end of their usable lifespan.
EB Finishes with Properties That Conform to Your Product Specifications
Whether your product is flat or three-dimensional, continuous or discrete, every clear or pigmented EB curable coating RDC creates will correlate to your specific requirements. This includes chemical resistance, scratch and abrasion resistance, weatherability, gloss, adhesion, and more. Whether your product is vinyl, wood, metal, plastic, or another specialty substrate, RDC Coatings can supply an optimal EB coating.
- Solid colors for particleboard, medium density fiberboard, aluminum, and fiber reinforced plastic (FRP)
- Low coefficient of friction (COF) coatings for treadmill decking
- Flooring coatings with electrostatic dissipative (ESD) and anti-skid properties
- Clear coatings for foil and paper
- Exterior coatings for signage
- Solid color and clear vacuum coatings for aluminum tubing
- Special effects coatings for store fixture applications
- Markerboard coatings
- Antimicrobial coatings
Your partner for sustainable, compliant energy-cured finishes
All RDC UV curable finishes are environmentally friendly and comply with globally accepted safety and sustainability standards, including…
- Low or No Volatile Organic Compounds (Low-VOC/Zero-VOC)
- California Air Resources Board (CARB) Compliant
- American Innovation and Manufacturing (AIM) Act Compliant
- Meets or exceeds American National Standards Institute (ANSI), Kitchen Cabinet Manufacturers Association (KCMA), and Scientific Equipment and Furniture Association (SEFA) Testing Requirements
How can RDC Coatings help you?
Manufacturers in multiple industries apply RDC Coatings’ custom formulations to a wide variety of materials and products. Leverage RDC Coatings’ 35-plus years of experience in engineering, developing, and manufacturing custom, energy-cured coatings to address your unique needs.