Lab Capabilities
Your optimal, environmentally-friendly coating chemistry is formulated, tested, and verified through RDC’s in-house laboratories.
RDC Coatings utilizes materials science to manipulate the properties of coating chemistries and generate your ideal energy-cured solution.
Every custom, energy-cured coating formulated by RDC’s chemists and engineers leverages materials science. By understanding and manipulating the properties of the chemistries and materials utilized to create your coating, RDC generates high-performance, sustainable, energy-cured solutions optimized to meet the parameters of your finished product. Each new commercial coating formulation passes through state-of-the-art laboratories at RDC’s 35,000-square-foot facility.
Development Laboratory
In RDC’s development laboratory, a sample of your finished product is subjected to destructive testing. This enables a thorough analysis of your existing coating and substrate to determine its chemical composition and resulting finish properties. Those findings inform the chemistries used in a prospective formulation.
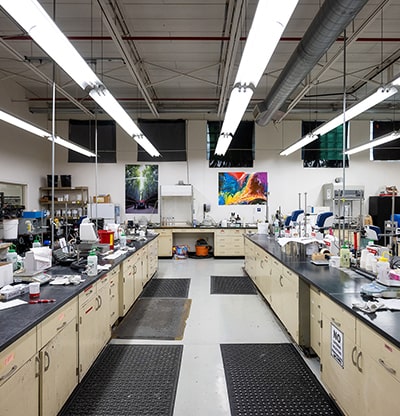
Application Laboratory
Based on the details collected by RDC’s team during their initial line audit, a precise replication of your production line process is set up in the application laboratory. The lab houses multiple application methodologies, including roll coating, spray coating, curtain coating, and vacuum coating. RDC recently invested in a new ultraviolet (UV) curing conveyor equipped with microwave, gallium-, mercury-, and iron-based LED; ARC; and Excimer lamps. This enables RDC to match the dosage produced by your curing system in the laboratory.
The formulation created in the development lab is applied to your substrate at the required thickness and energy cured. Then, the sample’s properties are evaluated to assess its alignment with your parameters. Tests include verification of proper adhesion, degree of gloss, resistance to stains, chemicals, or abrasions, flexibility and more. Pending the results of these tests, additional formulations may be developed and the testing process repeated until the optimal chemistry is achieved.
Samples of the prospective coating formulation applied to your substrate are delivered to you for evaluation. Upon approval, a sample batch of the coating is pilot-tested at your facility on your production line to verify its performance. If the coating meets all required parameters, it moves into our manufacturing process.
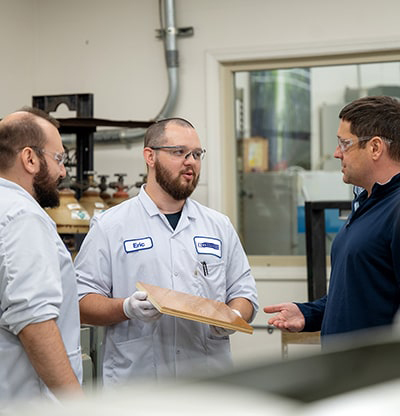
Quality Control Laboratory
As a total quality company, RDC Coatings follows a strict process to ensure consistency among every product manufactured for our customers. Your custom coating will be regularly sampled and examined by our quality control lab to ensure that every batch you receive is consistent.
Additionally, RDC sources the raw materials used in its custom coating formulations from multiple suppliers. This strategy prevents supply chain disruptions from affecting the manufacturing of your solution. In fact, during the pandemic, RDC was able to continuously supply all of its customers with their coatings and finishes with no interruptions.
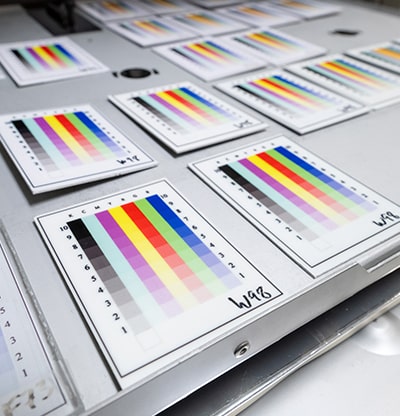
Your partner for sustainable, compliant energy-cured finishes
All RDC UV curable finishes are environmentally friendly and comply with globally accepted safety and sustainability standards, including…
- Low or No Volatile Organic Compounds (Low-VOC/Zero-VOC)
- California Air Resources Board (CARB) Compliant
- American Innovation and Manufacturing (AIM) Act Compliant
- Meets or exceeds American National Standards Institute (ANSI), Kitchen Cabinet Manufacturers Association (KCMA), and Scientific Equipment and Furniture Association (SEFA) Testing Requirements
How can RDC Coatings help you?
Manufacturers in multiple industries apply RDC Coatings’ custom formulations to a wide variety of materials and products. Leverage RDC Coatings’ 35-plus years of experience in engineering, developing, and manufacturing custom, energy-cured coatings to address your unique needs.