Plastics
Boost your plastic products’ resilience and durability with custom, energy cured coatings.
Environmentally friendly finishes from RDC Coatings are applied to a diverse range of plastic formulations.
Plastic manufacturers utilize finishes engineered by RDC Coatings to improve the appearance, durability, and scratch resistance of their products. RDC’s custom coating formulations are used on a diverse range of plastic products including flooring, entertainment media like CDs and DVDs, films, and road reflectors. RDC engineers and supplies energy cured coatings that provide superior adhesion to acrylic, composite, polycarbonate, polypropylene, polystyrene, hybrids, and more.
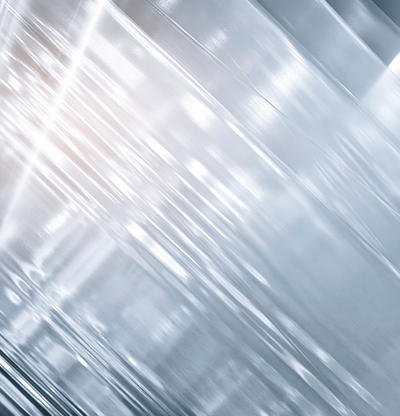
Benefits of your RDC Coatings’ energy cured plastic finish.
When it’s created and supplied by RDC Coatings, your custom formulated plastic coating will meet each one of your parameters. Your finish will be engineered to match the specifications of your production process, application and curing equipment, environment, and product.
Plastic Finishes That Streamline Your Production Process
Looking to enhance your current coating formulas, expand your finish offerings, or create a new production line? Whatever your plastic finish needs, RDC Coatings always supplies customer-focused expertise with every coating formulation. You’ll experience an on-site process audit that allows RDC to gain comprehensive insight into your production line and plastic product. Based on those details, RDC’s engineers create a custom finish for your plastic product that is validated in state-of-the-art testing labs. Additionally, RDC provides ongoing process management and technical support.
Plastic Coating Formulations Tailored to Your Application Equipment
RDC Coatings’ solutions for plastic products are engineered to improve the operation of your application equipment. Each coating’s rheology is fine-tuned to flow smoothly and evenly through your roll coating, spray coating, curtain coating, or vacuum coating equipment. For even greater efficiency and throughput, your coating formulations can be supplied in a variety of container sizes.
Plastic Finishes Developed to Maximize Your Curing Process
The chemistries used to formulate your ultraviolet (UV) curable coating, Excimer UV curable coating, electron beam (EB) curable coating, or water-based coating will produce fast curing, consistent finishes in less time. This reduces overall processing time while allowing for increased production volumes.
Plastic Coatings That Perform Dependably in Variable Environments
Not every production plant has climate control. That’s why RDC engineers your coating’s chemistry to perform consistently, regardless of the temperature or humidity. Use a UV curing process? RDC’s UV formulations accommodate differing UV lamp performances and photon outputs, whether the bulbs are brand new or at the end of their usable lifespan. This ensures consistency across production runs.
Plastic Finishes Created to Your Unique Requirements
Regardless of your plastic formulation, product shape, or application process, every coating RDC creates will meet your individual specifications. This includes resistance to scratches, abrasions, stains, and chemicals, as well as improved weatherability, degree of gloss, superior adhesion properties, and more.
Your partner for sustainable, compliant energy-cured finishes
All RDC UV curable finishes are environmentally friendly and comply with globally accepted safety and sustainability standards, including…
- Low or No Volatile Organic Compounds (Low-VOC/Zero-VOC)
- California Air Resources Board (CARB) Compliant
- American Innovation and Manufacturing (AIM) Act Compliant
- Meets or exceeds American National Standards Institute (ANSI), Kitchen Cabinet Manufacturers Association (KCMA), and Scientific Equipment and Furniture Association (SEFA) Testing Requirements
How can RDC Coatings help you?
Manufacturers in multiple industries apply RDC Coatings’ custom formulations to a wide variety of materials and products. Leverage RDC Coatings’ 35-plus years of experience in engineering, developing, and manufacturing custom, energy-cured coatings to address your unique needs.