Specialty Substrates
Unlimited energy cured coating options engineered to meet the unique parameters of virtually any substrate.
Bring your challenging, unusual, or unique substrates to RDC Coatings for a custom formulation that enhances durability, appearance, and your process.
In addition to creating coating solutions for wood, vinyl, plastic, and metal products, RDC Coatings is adept at solving challenges by developing energy cured formulations for other substrates.
Manufacturers with unique products and coating parameters leverage the expertise of RDC’s engineers and chemists to craft substrate-specific ultraviolet (UV) curable coatings, electron beam (EB) curable coatings, Excimer UV curable coatings, or water-based finishes.
Among the diverse range of products and substrates RDC has formulated coatings for are:
- Paper
- Composites
- Recycled materials
- Alternative energy components
- Raised pavement reflectors
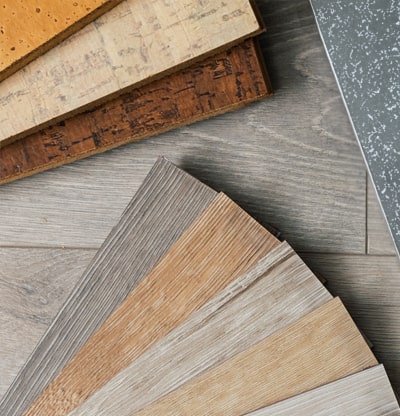
The following table summarizes the key benefits of partnering with a custom coating manufacturer like RDC Coatings for each specialty substrate type:
Substrate Type | Durability Benefits | Sustainability Benefits | Performance Benefits | Productivity Benefits | ROI Benefits |
---|---|---|---|---|---|
Paper | Increased resistance to moisture, grease, abrasion | Water-based options, enhanced recyclability, low VOC emissions | Improved barrier properties, tailored surface functionality, improved printing capabilities | Faster drying with UV/EB, increased line speeds | Reduced material usage, lower waste disposal costs, potential for premium pricing |
Composites | Superior protection against environmental degradation (moisture, UV, chemicals), enhanced wear resistance | Low/zero VOC options with UV/EB, reduced energy consumption during curing | Enhanced mechanical properties (abrasion, impact, flexibility), specific electrical properties | Rapid curing with UV/EB, enabling faster production cycles | Extended product lifespan, reduced maintenance and repair costs, higher production output |
Recycled Materials | Improved resistance to wear, scratches, and environmental factors | Supports circular economy initiatives, utilization of low/zero VOC coatings, energy savings | Enhanced aesthetic appeal, improved functional characteristics, increased material value | Efficient curing processes with UV/EB technologies | Lower raw material costs, increased product marketability, energy savings, reduced waste |
Alternative Energy | Long-term protection against erosion, corrosion (including salt water), UV degradation, and weathering | Low/zero VOC coatings, energy-efficient curing processes | Ensured long-term reliability, sector-specific performance enhancements (e.g., conductivity) | Faster curing with UV/EB, minimizing downtime for critical infrastructure | Extended lifespan of expensive components, reduced maintenance needs, consistent energy generation |
Raised Pavement Reflectors | Exceptional resistance to abrasion from traffic and snowplows, protection against UV fading and weathering | Utilization of low/zero VOC coatings | Maintained retroreflective properties under various conditions, long-term color consistency and visibility | Efficient and rapid curing processes | Extended service life, reduced frequency of replacements, enhanced road safety leading to fewer accidents |
The Growing Importance of Custom Coatings for Unique Substrates for Manufacturers
The manufacturing landscape is witnessing a significant shift towards the utilization of specialty substrates, driven by the pursuit of enhanced product features, sustainability goals, and economic advantages. These unique materials, distinct from traditional wood, plastic, metal, and vinyl, necessitate specialized coating solutions to fully realize their potential.
RDC Coatings stands at the forefront of this technological evolution, offering custom-engineered coatings tailored to meet the precise demands of these diverse substrates and leveraging decades of expertise to provide innovative solutions for manufacturers working with the substrates of tomorrow.
Benefits of RDC’s Custom Coatings for Specialty Substrates for Manufacturers
Advancing Sustainability in Manufacturing with RDC Coating Technologies
Environmental stewardship is a core principle at RDC Coatings, and every custom coating formulation is developed with a strong commitment to protecting and preserving the Earth’s resources. A key aspect of this commitment is the availability of low-VOC (Volatile Organic Compounds) and zero-VOC coatings, which minimize the release of harmful substances into the atmosphere.
Superior Performance: Tailored Coatings for Diverse Applications
RDC Coatings excels at customizing coating properties to precisely match the unique performance requirements of a wide range of specialty substrates, ensuring optimal functionality and longevity in diverse applications.
Boosted Productivity and Efficiency in Your Manufacturing Process
RDC Coatings offers manufacturers a range of coating technologies that boast exceptionally fast curing times. For example, ultraviolet (UV) coatings can cure in mere seconds, while Electron Beam (EB) coatings cure in fractions of a second. This significantly reduces the overall production time required for coated parts compared to traditional coating methods that can take hours or even days to fully cure.
Maximized ROI with RDC Coating Solutions
- Extended Product Lifespan: The superior durability provided by RDC Coatings’ custom-engineered formulations directly contributes to an extended lifespan for your products.
- Reduced Maintenance Costs: RDC Coatings’ durable coatings minimize wear and tear on specialty substrates, leading to a significant reduction in maintenance and repair expenses.
- Lower Energy Consumption: RDC Coatings’ Ultraviolet (UV) and Electron Beam (EB) curing technologies offer substantial energy savings compared to traditional thermal curing methods.
For industrial wood floor coatings and any other industrial floor coatings, contact us today.
Your partner for sustainable, compliant energy-cured finishes
All RDC UV curable finishes are environmentally friendly and comply with globally accepted safety and sustainability standards, including…
- Low or No Volatile Organic Compounds (Low-VOC/Zero-VOC)
- California Air Resources Board (CARB) Compliant
- American Innovation and Manufacturing (AIM) Act Compliant
- Meets or exceeds American National Standards Institute (ANSI), Kitchen Cabinet Manufacturers Association (KCMA), and Scientific Equipment and Furniture Association (SEFA) Testing Requirements
How can RDC Coatings help you?
Manufacturers in multiple industries apply RDC Coatings’ custom formulations to a wide variety of materials and products. Leverage RDC Coatings’ 35-plus years of experience in engineering, developing, and manufacturing custom, energy-cured coatings to address your unique needs.