Ultraviolet (UV) coatings
Your source for custom formulated, energy-cured Ultraviolet (UV) Coatings in any application.
Let RDC Coatings create the UV coating optimized for your needs.
No matter what type of UV lamp your manufacturing process uses — microwave, gallium, mercury, and iron-based, LED, ARC or others — RDC can formulate a highly durable UV coating that delivers superior performance. Your UV coating will be custom formulated to match your high-speed production line and product, including those made of vinyl, wood, metal, plastic, or any specialty material.
All RDC Coatings formulations, including your UV curable coating, are environmentally friendly and comply with globally accepted safety and sustainability standards.
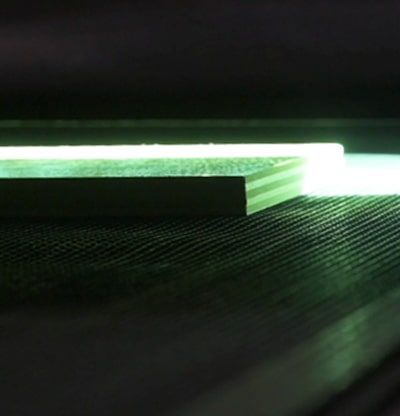
How does UV curing work?
UV curable coatings have a liquid-like feel and appearance that requires exposure to a UV light source to set as a solid. After the coating is applied in high-speed production lines by one of a variety of methods — including roll coating, spray coating, curtain coating, vacuum coating, and other coating processes — the product passes through a UV curing station. There, the UV light source causes a chemical reaction among the photo initiators in the coating. This reaction instantly transforms the coating into a highly durable, solid, dry polymer surface.
Why use custom-formulated UV-curable coatings?
RDC’s custom UV coatings help operations across a wide range of industries achieve versatile, high-performance finishes on diverse product types. Your RDC finish will deliver a range of advantages, including:
Rapid Curing and Increased Production Efficiency
UV coatings are often selected because of how quickly they cure. Thanks to their custom formulation, RDC’s UV coatings solidify in seconds, supporting extremely fast production cycles. This is a significant advantage over traditional coatings that require hours — or days — to cure through evaporation and/or the application of heat. This rapid curing dramatically speeds up production and enhances efficiency by cutting the amount of time products must spend on the manufacturing line. By enabling higher throughput, manufacturers can also optimize facility space usage, as they no longer need to allocate square footage for drying or curing areas. The faster curing speed of UV coatings also shortens lead times and minimizes the risk of defects caused by dust or debris settling on the coating before it hardens.
Environmental and Safety Advantages
Custom UV curable coatings from RDC are an environmentally friendly, sustainable option, primarily because they contain low to zero volatile organic compounds (VOCs). VOCs are harmful chemicals that can evaporate into the atmosphere, contributing to air pollution and posing health risks to workers. By eliminating VOC emissions, RDC’s UV-curable coatings help companies meet stringent environmental regulations and improve workplace safety. Additionally, the UV curing process does not require the high temperatures associated with traditional thermal curing, leading to significant energy savings and a reduced carbon footprint.
Superior Durability and Performance
Because the UV curing process creates a highly cross-linked polymer network, UV curable coatings offer exceptional durability and resistance to damage and wear. RDC’s tough, resilient UV coatings are formulated to be impervious to scratches, abrasions, scuffs, or chemicals. This durability is particularly beneficial in applications where product surfaces are exposed to harsh conditions, such as in residential and commercial flooring, cabinetry, millwork, hardwood plywood, furniture, and many others. The superior performance of UV-curable coatings can extend a product’s lifespan while reducing maintenance costs and the need to recoat.
Customization to Match Diverse Substrates
RDC can adjust your UV coating’s properties — such as hardness, flexibility, gloss, and adhesion — to meet the needs of different substrates and applications. This customization is especially valuable for finishing a diverse range of substrates, including plastics, metals, wood, vinyl, and specialty materials. This versatility makes them suitable for various applications, from flooring and cabinetry to plastics and millwork. RDC’s custom UV curable coatings adhere to different materials without compromising the integrity of either the coating or the substrate.
Substantial Cost Savings
Although the initial investment in UV curing equipment is not insignificant, the long-term cost savings can be substantial. The durability of RDC’s UV curable coatings reduces the need for reapplication, reducing both maintenance and material costs. The rapid UV curing process also cuts a manufacturer’s labor costs while increasing production output, making it a cost-effective solution for high-volume manufacturing environments. Additionally, the energy efficiency of UV curing — along with the elimination of VOC-related regulatory costs — contributes to overall cost savings.
Benefits of your RDC Coatings’ UV coating formulation.
When you partner with RDC Coatings, your UV curable coating solution is engineered to meet the unique specifications and requirements of your production process, application and curing equipment, environment, and product.
UV Cured Coatings Tailored to Your Production Process
Whether you’re looking to upgrade your current UV coating formula or designing a new manufacturing line, your UV finish is backed by RDC’s comprehensive, customer-focused expertise. These include initial, on-site process audits to gain a complete understanding of your production line and product. Based on those findings, RDC’s engineers develop a custom UV coating formulation that is subject to proof-of-concept validation in state-of-the-art testing labs. Additionally, RDC provides ongoing process management and technical support.
UV Curable Finishes Formulated for Your Application Equipment
RDC Coatings’ UV curable formulations are custom created to optimize their dispersal by your application equipment. Each coating’s viscosity is engineered specifically to flow smoothly and evenly through your roll, spray, curtain, or vacuum coating dispenser. Further, for easy, error-proof filling of dispensers, your UV coating solution is supplied pre-mixed; no additives or on-site blending required.
UV Cured Finishes Designed for Your UV Curing Lamps
The chemistries used to produce your UV curable coating are activated by photons from any of the full spectrum of conventional UV lamps. These include microwave, gallium, mercury, and iron-based, LED, ARC or others, including Excimer UV.
UV Coating Formulations That Perform Consistently in Your Variable Environment
RDC Coatings understands that not every manufacturing facility is climate controlled. Therefore, your UV curable coating’s chemistry is engineered to perform consistently across a broad range of temperatures and humidities — from high to low. Additionally, RDC’s UV formulations are designed to accommodate variable UV lamp performances and photon outputs, whether the bulbs are brand new or at the end of their usable lifespan.
UV Finishes with Properties That Conform to Your Product Specifications
Whether your product is flat or three-dimensional, continuous or discrete, every UV curable clear or pigmented coating RDC creates will match your specific requirements. This includes chemical resistance, scratch and abrasion resistance, weatherability, gloss, adhesion, and more. UV coatings can also be customized to match your product’s material, including vinyl, wood, metal, plastic, or specialty substrates.
- Resilient flooring
- Flexible vinyl films
- Polyolefin flooring
- Tie coats for adhesion promotion
- Luxury vinyl tile (LVT) coating system
- UV stains, fillers, and sealers
- Scratch resistant and self sealing UV top coats
- Spray and vacuum UV coatings for moldings
- Sprayable, solvent based UV clears and UV white coatings
- Sprayable solvent based UV white coatings
- Sprayable 100% solids UV clear coatings and UV white primers
- Styrene-free fillers
- Spray and abrasion resistant coatings for flooring
- Adhesion promoting primers
- Toned UV top coats
- Antimicrobial coatings
- Field-applied, high clarity, water-based UV coatings
- Pigmented spray coatings for automotive applications
- Toned top coats for aluminum panels
- Vacuum coating for tubing and pipe
- Pigmented and clear coatings for aluminum
- Vacuum coating for tubing and pipe
- Resilient flooring
- Flexible vinyl films
- Polyolefin flooring
- Tie coats for adhesion promotion
- Luxury vinyl tile (LVT) coating system
Your partner for sustainable, compliant energy-cured finishes
All RDC UV curable finishes are environmentally friendly and comply with globally accepted safety and sustainability standards, including…
- Low or No Volatile Organic Compounds (Low-VOC/Zero-VOC)
- California Air Resources Board (CARB) Compliant
- American Innovation and Manufacturing (AIM) Act Compliant
- Meets or exceeds American National Standards Institute (ANSI), Kitchen Cabinet Manufacturers Association (KCMA), and Scientific Equipment and Furniture Association (SEFA) Testing Requirements
How can RDC Coatings help you?
Manufacturers in multiple industries apply RDC Coatings’ custom formulations to a wide variety of materials and products. Leverage RDC Coatings’ 35-plus years of experience in engineering, developing, and manufacturing custom, energy-cured coatings to address your unique needs.